The Goleta: Traditional Wooden Boats of the Canary Islands
The Canary Islands, an archipelago adrift in the Atlantic, possess a rich maritime heritage deeply intertwined with their unique geography and history. Among the most iconic vessels born from this tradition is the goleta, a traditional wooden boat that embodies the ingenuity and skill of Canarian boat builders. This article delves into the story of the goleta, examining its design, construction techniques, and the challenges it faces in a modern world.
A Boat Shaped by the Atlantic
The goleta’s evolution is inextricably linked to the Canaries’ role as a crucial stopover point for ships sailing between Europe, the Americas, and Africa. Demand for reliable cargo carriers led to the development of a distinctive boat design capable of handling the often-turbulent Atlantic waters. Unlike many European boats of the time, the goleta typically features a relatively short, broad beam, and a high bow – adaptations necessary to navigate the unpredictable conditions and carry valuable cargo. The “goleta” designation itself is debated, with theories linking it to Dutch influence or simply a regional descriptive term. The fundamental principles of boat construction involved techniques often shared across regions, with variations arising from local resources and specific maritime needs. For example, the overlapping planks found in boats like the clinker hull, a construction method more common in northern Europe, offer a comparison to the methods used in Canarian boat building, highlighting both similarities and differences in response to varying environmental challenges and available materials.
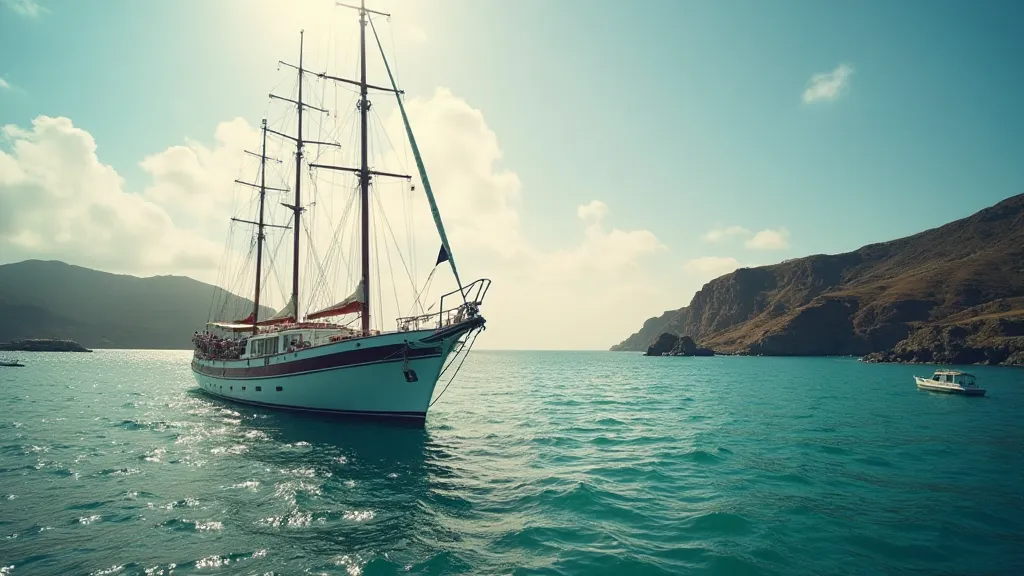
The Art of Canarian Boat Building: A Regional Craft
The construction of a goleta was, and remains, a testament to Canarian craftsmanship. Traditionally, the process was entirely reliant on local resources. Timber, primarily Canarian pine (Pinus canariensis), was carefully selected and seasoned. The skills were passed down through generations, often within families, with each individual specializing in a particular task – from frame-making to planking and rigging. The keel, carefully shaped, forms the backbone of the vessel. Frames are then assembled, defining the shape of the hull. Planking, a meticulous process, involves overlapping planks of wood, each carefully fitted to the frame, creating a watertight hull. Tar, made from pine resin, was used to seal the seams.
The use of traditional tools, hand planes, saws, and chisels, further emphasized the craftsmanship involved. The entire process demanded precision, patience, and a deep understanding of wood properties and naval architecture. The sails, traditionally made of canvas, were expertly crafted to maximize efficiency in the prevailing winds. The rig was carefully designed to take advantage of the trade winds that consistently blow through the Canary Islands. The way the hull is built, whether through overlapping planks or a more direct approach, significantly impacts the boat’s strength and maneuverability. A deeper understanding of these building methods is often appreciated when considering the complexities of boat design, similar to how the carvel hull offers a different, yet equally valuable, approach to achieving a watertight and durable vessel.
Regional Variations and Innovations
While the core design principles remained consistent, regional variations in goleta construction existed throughout the Canary Islands. Each island, with its own microclimate and local timber resources, contributed to subtle differences in hull shape, sail configuration, and overall dimensions. For example, goletas built on La Palma, known for its steep terrain, often featured a slightly different bow shape adapted for navigating closer to the coastline. Fuerteventura, with its strong winds, saw boats with reinforced rigging. These differences weren't merely aesthetic; they reflected a nuanced understanding of local conditions and the practical considerations of shipbuilding.
The Materials: Canarian Pine and the Art of Seasoning
The heart of any goleta lay in the quality of its timber. Canarian pine, with its strength and durability, was the wood of choice. However, simply felling a tree was only the beginning of the process. Proper seasoning was absolutely crucial. The wood would be carefully stacked and allowed to dry naturally, a process that could take many years. This slow drying process minimized the risk of warping and cracking, ensuring the long-term structural integrity of the vessel. The knowledge of how to select and season timber was passed down through generations, a vital component of the overall shipbuilding craft.
Comparing Goletas to Traditions Elsewhere: The Barra and the Topaz
The Canarian goleta isn't an isolated example of maritime ingenuity. Across Europe and beyond, traditional boatbuilding communities developed vessels perfectly suited to their own environments and needs. Looking at traditions elsewhere offers valuable context. For example, the barra, a traditional Portuguese fishing boat, shares a similar purpose – navigating coastal waters – but demonstrates unique design features born from the Portuguese maritime heritage. Similarly, the Topaz, a distinctive wooden boat from Brittany, France, provides another fascinating comparison, showcasing the diverse approaches to boatbuilding across Europe.
Challenges and Preservation Efforts
The rise of modern, mass-produced vessels has significantly impacted the traditional goleta shipbuilding industry. The cost and time involved in building a traditional boat are considerably higher than constructing a modern fiberglass or steel hull. As a result, the number of working goleta shipyards has dwindled significantly. However, a renewed interest in preserving this unique cultural heritage has emerged.
Several organizations and individuals are working to keep the tradition alive. These efforts include:
- Apprenticeship Programs: Some shipyards are offering apprenticeships to younger generations, passing on the traditional skills.
- Restoration Projects: Existing goletas are being carefully restored to their former glory.
- Documentation: Historians and maritime enthusiasts are documenting the history and techniques of goleta construction.
- Cultural Events: Festivals and regattas showcasing traditional boats help raise awareness and appreciation.
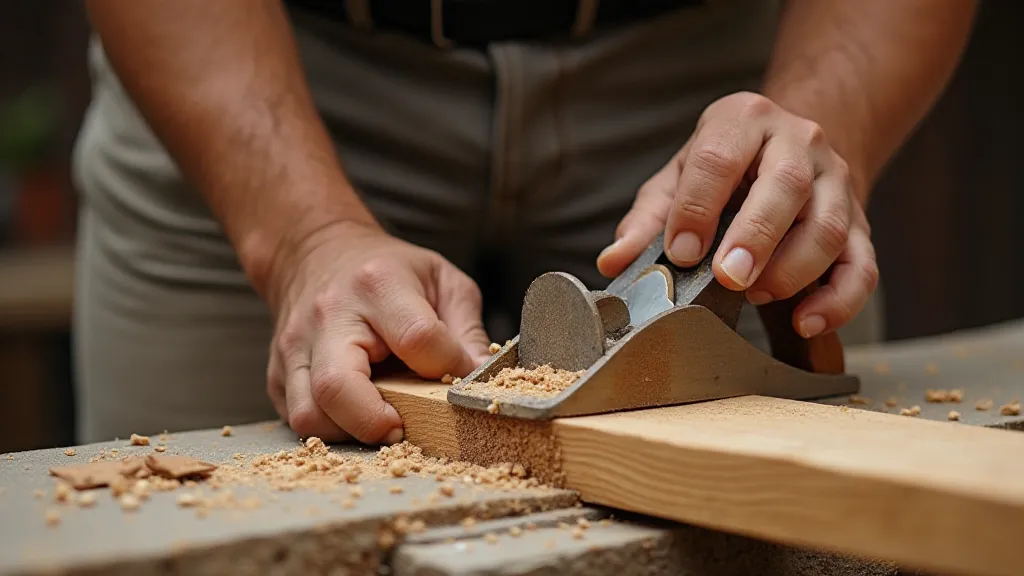
The Future of Goleta Shipbuilding: Sustainability and Revival
The challenges facing goleta shipbuilding are not merely economic; they's deeply intertwined with the broader shift towards mass production and disposable goods. However, a growing awareness of the environmental and cultural costs of this model is fueling a revival of traditional crafts. The use of sustainable materials and the revival of traditional skills are becoming increasingly important. There's also a growing interest in eco-tourism, with visitors seeking authentic experiences that connect them to the local culture and environment. This could create new opportunities for goleta shipyards, but it will require a concerted effort to adapt to changing market demands.
Beyond the Hull: The Rigging and Sailing of the Goleta
The goleta’s beauty wasn't solely defined by its hull; the rigging and the art of sailing were equally important. The sails, meticulously crafted from canvas, were designed to capture the prevailing trade winds. The sailors possessed a deep understanding of the winds and currents, using their knowledge to navigate the Atlantic with skill and precision. The dance between the wind and the sails was a breathtaking sight, a testament to the harmony between humans and nature.
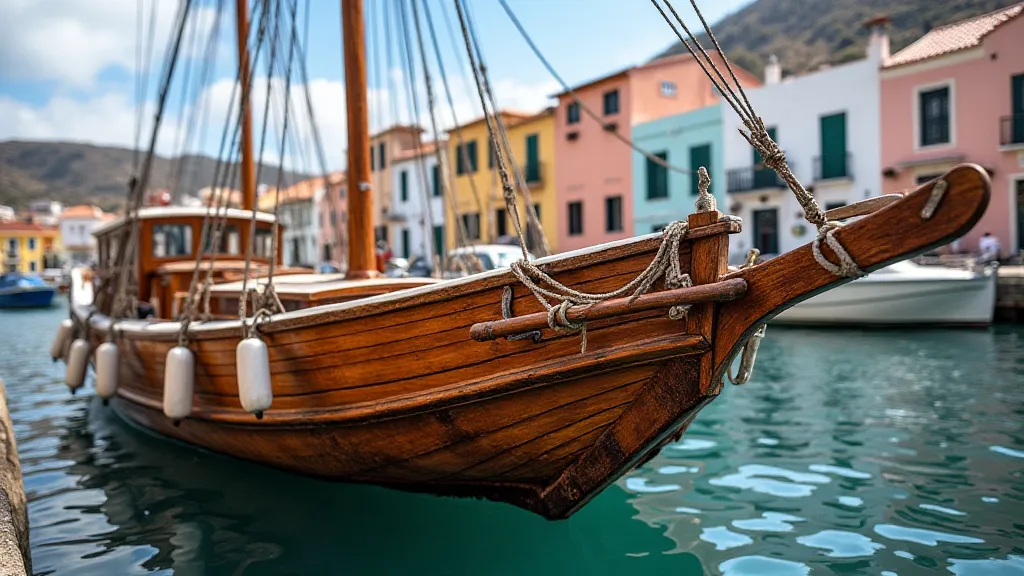
A Living Legacy
The goleta of the Canary Islands represents more than just a boat; it is a symbol of resilience, ingenuity, and a deep connection to the sea. While the future of traditional goleta construction remains uncertain, the ongoing preservation efforts offer hope that this iconic vessel will continue to grace the waters of the Canary Islands for generations to come. The story of the goleta serves as a powerful reminder of the importance of safeguarding cultural heritage and celebrating the skills of traditional craftsmen.